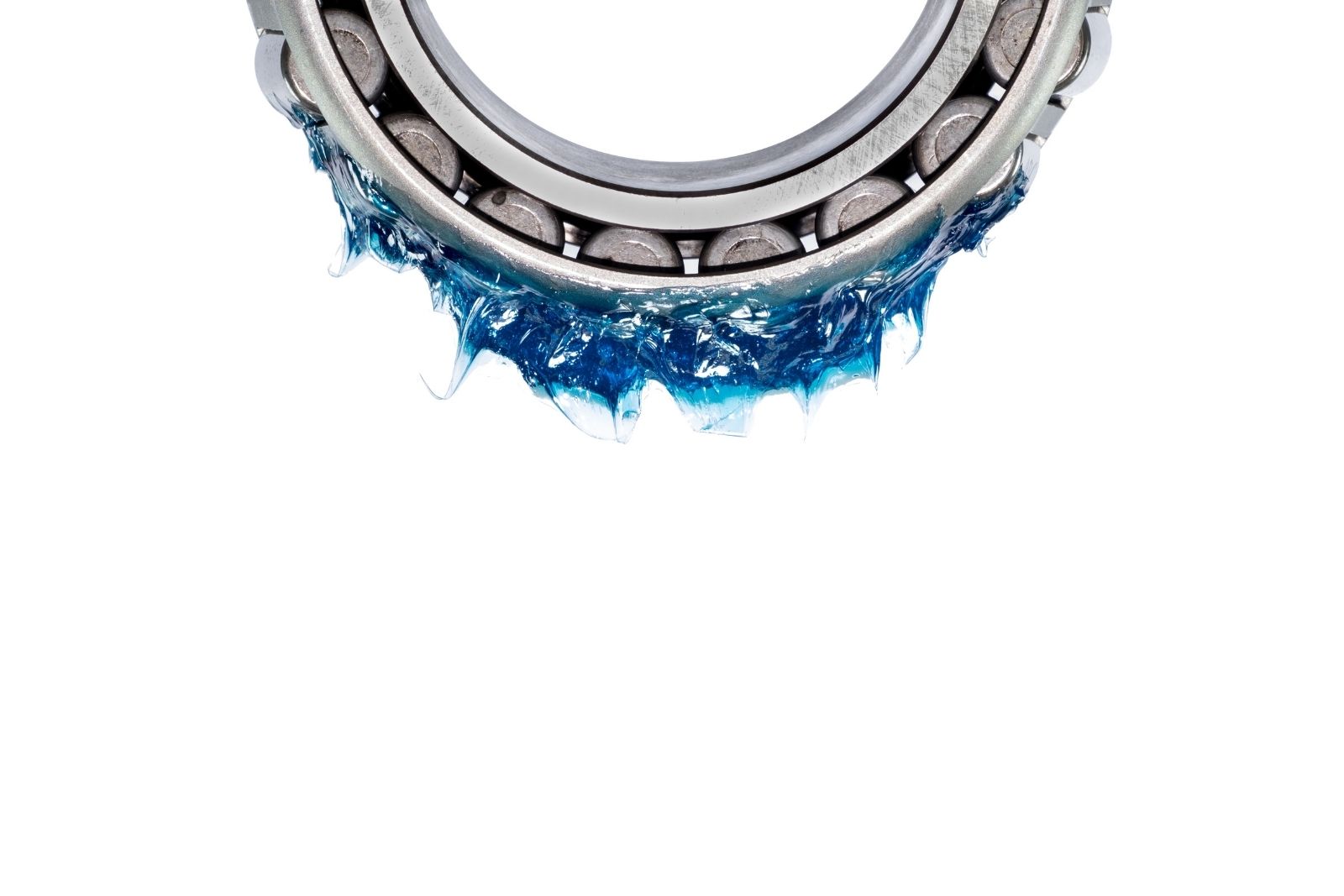
Degreasing of metal parts
The metal degreasing process is an essential cleaning measure for business productivity because it returns an object free of any contamination resulting from previous production cycles. The type of degreasing to be carried out varies based on numerous factors and may require specific machines based on the treatment. To achieve the desired result, it is necessary to know the basic elements that are involved in the fat removal process.
Table of contents
1. Degreasing: what it is and how it works
Metal parts and surfaces are some of the most frequently degreased equipment in industrial workplaces: from the removal of light accumulations of oil to the cleaning of accumulations of grease that are deposited on the various components.
Removing all grease residues is not simply a matter of thorough cleaning, but rather the destruction of every single oily molecule. This chemical-physical process differs from normal washing and cleaning since it aims to eliminate light or heavy, synthetic or natural, refined or raw oils, thus leaving the surface of the piece clean and free.
Degreasing precedes many processes such as pickling, passivation and polishing, because it allows to obtain a surface uniformly prepared for subsequent treatments.
Incorrect or insufficient degreasing could potentially create corrosion problems during subsequent processing of a particular product.
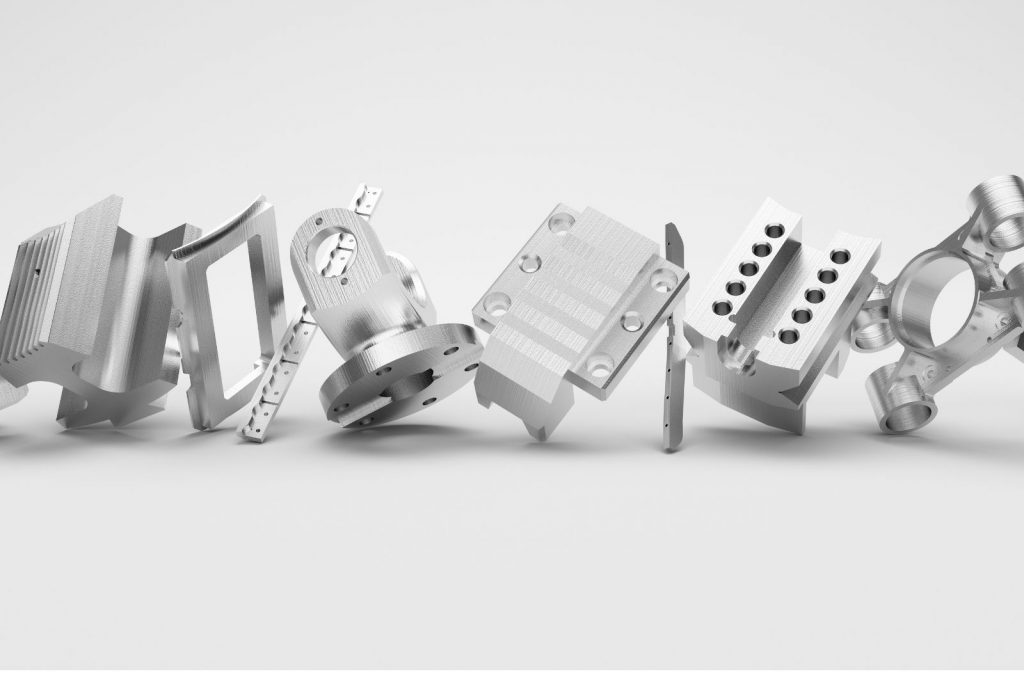
The choice of the degreasing process for the various products is determined by the following factors:
1- Type of metal: the materials of the pieces can be iron (steels with different carbon content), stainless steel, cast iron, aluminum and its alloys, copper and its alloys (brass, bronze, nickel silver, etc.), zinc and its alloys and others. Slightly alkaline solvents are used for aluminum and non-ferrous metals, while stronger alkaline solutions are required for steel and stainless steel.
2- Type of grease or oil to be removed: the removal of greases, lubricants and anticorrosive oils may involve the use of solvents of different nature and the use of specific machines.
-3 Degree of contamination: for example, there may still be chips or other residues on the workpiece.
In addition, another deciding factor is the technology and capabilities available for degreasing.
2. Tools for the degreasing process
To maximize the effectiveness of the degreasing of the pieces, the best method of washing the pieces must be performed and at the same time the most effective degreasing solvent must be used.
When it comes to choosing a parts washing method, your best bet may be to use a parts washer. Industrial parts, due to their highly detailed design often featuring complex contours, can be extremely difficult to clean by hand. Since the system of parts washing machines applies the cleaning solvent evenly over the entire surface, even the most complex elements of the piece do not hinder a complete and homogeneous cleaning.
In addition, industrial-grade parts washers excel at removing heavy build-up of grease in a short period of time without compromising the integrity of the parts they clean.
The basic types of degreasing processes are listed below.

Spray cleaning or rinsing of the pieces: cold degreasing involves the use of a physical and mechanical agent, such as the cleaning power of high pressure jets or the use of a dispensing brush.
The surface of the metal is thus rinsed. This doesn’t just result in degreasing. Other debris and dirt, such as shavings, are also removed from the workpiece. This type of degreasing involves chemical and mechanical cleaning.
Immersion baths/ Dip Washing: metal degreasing tanks are usually used where the alloy is immersed in chemical solutions that can be heated to a certain temperature (depending on the chemicals and the material). The high temperature used with this method can reduce the immersion time as it increases the rate of chemical reactions.
Steam degreasing: Steam degreasing is suitable for parts that are only slightly contaminated with grease and oil. The degreasing process is carried out in a chamber. The product is heated to boiling and the steam is then directed onto the cold piece. In this case the steam condenses and the solvent condensate is used to rinse the surfaces.
Vibration Cleaning: No chemicals or aqueous solutions are required in vibratory cleaning. The pieces are instead “vibrated”. The frequency of the vibrations exceeds the attraction force of grease, oils, shavings and other residues on the metal. Dirt and lubricants are “wiped out” and then sucked up. No solvents are required, which has a positive effect on costs and the environment.
3. Problems that can be encountered during degreasing
Degreasing is an essential step before other processes such as coating, printing or varnishing, but is sometimes associated with challenges and problems. These include, the choice of the appropriate procedure, the efficiency of the process, the costs for the recovery of the oils.
Recycling costs, for example, if chemicals are used for degreasing, do not always have to be disposed of immediately after use. It is also possible to recycle them. However, the procedures involved for recycling involve additional costs, for example, costs for safe packaging, transport and reprocessing.
Costs can therefore vary according to the type and quantity of chemicals used for degreasing. The same goes for the disposal of chemicals if they cannot be reprocessed.
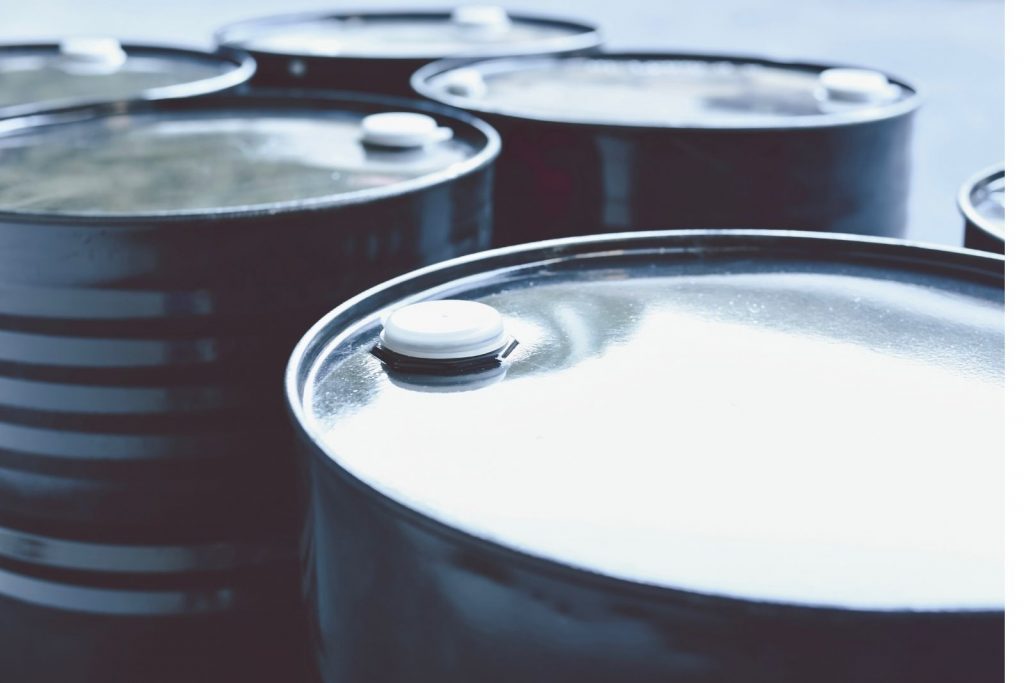
In conclusion, the surfaces of components contaminated with oil and fat residues can compromise the efficiency and quality of a production process. For this reason, degreasing is one of the most common industrial cleaning operations. Virtually every company and organization that uses grease-storing equipment must perform degreasing to keep the equipment in ideal condition for its application.